Labor Management in the SAP EWM application provides several features for a warehouse to plan, monitor, and utilize resources efficiently. The performance of employees in a warehouse can also be evaluated in the SAP EWM Labor Management by comparing the planned time versus the actual time. Labor Management can also be connected to an external Human Resource system where the labor utilization data is sent that can further be used in performance evaluations.
Functions of SAP EWM Labor Management
The various functions of the EWM Labor Management are shown in the diagram below:
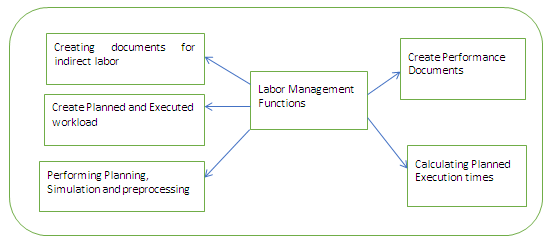
Planned and Executed Workload
Every activity in the warehouse process has a certain workload. This workload can be planned based on the scope of the task. For example: for a warehouse order, SAP EWM creates a document for the planned workload which is a basis for resource planning. After the work is executed, additional data like the start and finish times are used to calculate the executed workload. The executed workload is then used to compare with the planned workload to calculate the efficiency. Like the warehouse orders, this can also be done for the following warehouse processes:
- Warehouse orders. (WO)
- Value-added service orders
- Quality inspection documents
- Physical inventory documents
- Indirect labor
Indirect Labor Management
The tasks which are not directly related to the standard warehouse activities are called Indirect Labor. An executed workload document for indirect labor is automatically created after the completion of the task, which enables the evaluation of indirect labor with direct labor. This evaluation is done in the warehouse management monitor for executed workload and is used further for the creation of employee performance documents.
Planning, Simulation, and Pre-processing
Planning and pre-processing give an overview of the workload for the tasks related to inbound and outbound deliveries or in the physical inventory. Once the warehouse tasks, QM inspection, or physical inventory documents are created, the planned workload documents can be used in operational planning. These can be used to define calculated planning goals based on the workload or processors and simulate the output.
Performance Documents
A performance document has the details of planned and actual execution durations of the assigned workload. This helps in evaluating the performance or utilization of the employee.
SAP EWM Labor Management Activation
The Labor Management is activated by customizing at the warehouse level. Once this is activated at the WH level, the next step is to activate the labor-management for internal process steps (pre-defined by SAP), and the external process steps (defined by the customer). This helps to plan, track, and measure the labor times for all those warehouse processes.
If several external process steps are linked to the same internal process step, then all these external steps are activated for labor-management by single activation of the internal process step. For example: in the warehouse tasks for the Process-Oriented Storage Control, the external process steps are determined from the storage process set-up. The system thus creates a record for the planned workload for each step in the POSC.
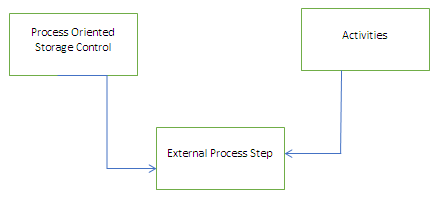
Configuring Processors
The processor master data is created as a Business Partner (BP) to use in SAP EWM Labor Management. All the warehouse processes applicable for labor-management are then assigned to this processor with the role LM0001 in BP. The processor could be a forklift operator or a picker on foot. All the relevant personal, supervisor, and shift information are maintained for this processor in the identification and labor-management attribute tab of BP. The optional entries like processor type, the reporting group, and the work category can also be maintained for indirect labor tasks and reporting purposes.
Configuring Shift Management
Shift Management can be set up under SAP EWM Labor Management to plan work schedules for resources by centrally defining shifts and shift sequence. This will be used further to determine labor productivity, efficiency, and performance in any given shift in the warehouse by recording the processor’s shift in the warehouse order once WO is confirmed.
A processor’s shift and shift sequence are defined with a start date and end date. In addition, available working time can be determined by taking break patterns and non-productive time (such as administration, cleaning, and meetings) into account. This is called a shift factor. Shift assignments and shift lead for each shift can then be done in the warehouse monitor where multiple processors are assigned to a shift and sequence.
The work schedule is maintained in the warehouse monitor under shift management where attributes like overtime work, leaves, breaks, capacity, etc., can be recorded for each processor.
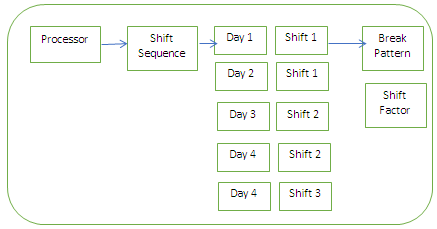
Time and Attendance in the EWM Labor Management
The IN/OUT Time and Attendance of each processor can be maintained in the EWM Labor Management. This can either be generated in EWM or interfaced through an external time and attendance system. This data is then used to find out who is available in the shift and also the monthly/yearly productivity of each processor.
Engineered Labor Standards (ELS)
An ELS is used to find out the normal time required for the execution of any warehouse activity. The normal time is the expected time under normal circumstances as per the standard operating procedure. It is initially calculated when the planned workload is generated as planned duration. After the resource is assigned to a warehouse order and executed workload is generated, this time is calculated again as adjusted planned duration. The standard time required to execute a warehouse activity is then calculated by multiplying the adjusted planned duration with the PFD factor (Personal needs, Fatigue, and unavoidable Delays). This time is then stored in the executed workload.

Calculating Travel Distance and Travel Time
SAP EWM Labor Management will calculate the distance that a warehouse operator needs to travel to execute a warehouse order. This is used to calculate the latest start time for a warehouse order and normal time using ELS. The travel distance can either be direct distance or distance based on the networks considering edges and nodes where the processor moves across the available routes.
Final Notes
The SAP EWM Labor Management application, as outlined above, helps in the proper utilization of warehouse employees, thereby being very useful for an organization to efficiently plan and execute the warehouse processes and tasks. It also helps cut down the labor cost by employing a more suitable use for workers in assigning and executing warehouse activities.
—
Did you like this tutorial? Have any questions or comments? We would love to hear your feedback in the comments section below. It’d be a big help for us, and hopefully, it’s something we can address for you in the improvement of our free SAP EWM tutorials.
Navigation Links
Go to the next lesson: SAP EWM RF Framework
Go to the previous lesson: SAP EWM Picking Process
Go to overview of the course: SAP EWM Training