Welcome to the tutorial about SAP MRP types. SAP MRP types are necessary to define which MRP procedure can be used for planning a particular material as well as restrict MRP related parameters permitted in material master records. This tutorial is part of our free SAP MM course.
SAP MRP type is a field that is maintained in the material master MRP 1 view under MRP procedure data. This is a key which is used to regulate the material requirements planning. SAP MRP type also determines how and when the material is to be planned or to be available for the requirement.
MRP procedure used for planning a material is determined with the help of SAP MRP type and this also determines the value or settings to be maintained in the other MRP views.

There are several SAP MRP types that have been defined in the standard SAP. Please find below the list of standard SAP MRP types:
- ND – No Planning
- PD – MRP
- R1 – Time-phased planning
- VB – Manual reorder point planning
- VM – Automatic reorder point planning
- VV – Forecast-based planning
There are also other SAP MRP types available. SAP MRP types can be configured based on the business requirements. SAP MRP types can be customized in the IMG activity and then the same MRP type can be assigned to the required material.
Customizing for SAP MRP Types
Here is the path in SPRO transaction:
IMG -> Materials Management -> Consumption-Based Planning -> Master Data -> Check MRP Types -> Execute
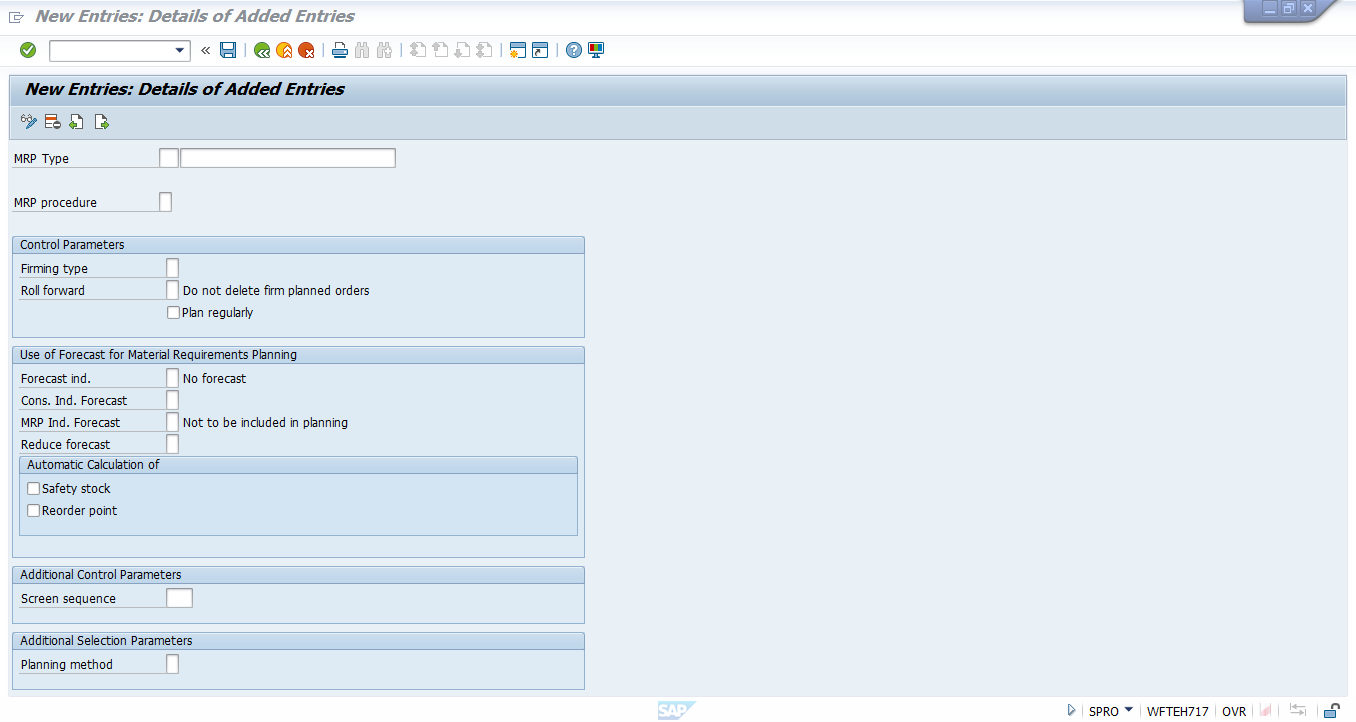
MRP Type – This field should contain the name for the MRP type and the description for it should be typed in the next field. When a customizing takes place, the name or parameter would begin with Z. But still this would be based on the business requirement and it could be configured to suit as per the business.
MRP Procedure – The MRP procedure used for planning the material is maintained in this field. Some of the procedures are:
- B – Reorder point planning
- D – Material requirements planning
- N – No MRP
- S – Forecast-based planning
- R – Time-phased materials planning
- X – Without MRP, with BOM explosion
Firming type – The procurement proposals that comes as an output of a planning run would need to be firmed and scheduled in the planning time fence. This firming type determines the firming of procurement proposals within the stipulated planning time fence. The below are the firming types:
- 0 – Planning results not firmed
- 1 – Automatic firming and order proposals rescheduled out
- 2 – Automatic firming without order proposal
- 3 – Manual firming and order proposals rescheduled out
- 4 – Manual firming without order proposal
The firming date could also be entered manually during the planning run. As a result of this the planning time fence would be extended to the manually entered firming date.
Roll forward – Two settings pertaining to planned orders could be maintained in this field. One is to delete firm planned orders and the other is not to delete firm planned orders. This indicator helps to delete or not delete the planned order during planning run. New planned order could also be generated based on the materials requirements at the time of planning run.
Forecast indicator – This indicator is used to determine whether forecast results would need to be included in materials requirement planning or not. The options that are available for this field are:
- No forecast
- Obligatory forecast
- Optional forecast
Consumption indicator of forecast – This indicator is used to determine which consumption values are to be considered for forecast. The consumption values are total consumption and unplanned consumption. Either of these two consumption values are maintained in the consumption indicator forecast.
MRP indicator of forecast – During planning run or net requirements calculation it should be predetermined to include forecast value for net requirements calculation. If forecast values are to be included for net requirements calculation, then it should be determined unplanned requirement or total requirement.
Reduce forecast – With this indicator the forecast requirement could be controlled for reduction. Reduction of forecast requirement by consumption, reduction of forecast requirement in current month, average reduction of the forecast requirements. So, any of these three values could be selected and maintained in reduce forecast field.
Automatic calculation – Automatic calculation of safety stock and reorder point could also be maintained in the MRP types customization. The indicator must be set if the safety stock and reorder point are to be calculated automatically. For net requirements calculation, safety stock and reorder point value would be needed.
The above described are the major fields that would need to be maintained in SAP MRP type customizing. Standard SAP MRP types are available, which could be copied, customized and configured to suit our business needs. SAP MRP type could be created by copying from the existing one and changing the required fields. The newly created SAP MRP type would be made available in the drop down of SAP MRP type field in a material master and the required type could be set against the material in the MRP view.
MRP Scenario 1
If a material is to be removed from MRP or not to be planned automatically, procurement proposals are not required to be created automatically. Then, MRP type could be set to ND – No planning. When ND is set up in the MRP type of MRP1 view, the material would not be considered for planning run either at a plant level or MRP area level. The other parameters like forecast, consumption would be considered from the MRP type customization.
MRP Scenario 2
If a material is to be planned for MRP, procurement proposals would need to trigger automatically, which could then be converted to either a planned order or a purchase requisition. The MRP type to be set in material master is PD, the other MRP parameters like forecast, consumption values, MRP procedures would be considered for planning run from SAP MRP type configuration.
MRP Scenario 3
If a material is to be planned based on the past historical consumption data, then consumption-based planning would need to be set up for that material. If the reorder point based planning is to be setup, then MRP type should be either VB or VM. If forecast-based planning is to be carried out, then MRP type VV should be maintained. If time-phased planning is to be carried out, then R1 would need to be setup. Apart from the MRP type field, for the planning run to be executed successfully and the exact net requirements to be calculated, the other MRP parameters like reorder point, safety stock, forecast values, consumption data, BOM explosion, lot size calculation and the other fields required for planning run would need to be maintained in the material master. Material master data maintenance in all the four MRP views is important for successful execution of planning run and net requirements calculation.
—
Did you like this SAP MM tutorial? Have any questions or comments? We would love to hear your feedback in the comments section below. It’d be a big help for us, and hopefully it’s something we can address for you in improvement of our free SAP MM tutorials.
Navigation Links
Go to next lesson: SAP MRP Profile
Go to previous lesson: SAP MRP Procedures
Go to overview of the course: SAP MM Training
We are struggling with PD MRP type items not ordering just in time like V1 stocked items using the PDT on the material master. Instead they are ordering at the time the work order is released, even if the basic start date is 6 mos down the road. Is there a setting on the MRP type that will allow planned on demand (PD) materials to use the PDT to trigger MRP? Hopefully this explanation is clear enough.
Can someone tell me what is a “mini mrp” I had someone tell me they ran a mini mrp in sap and I don’t know what this is.
Thank you
We are struggling with PD MRP type items not ordering just in time like V1 stocked items using the PDT on the material master. Instead they are ordering at the time the work order is released, even if the basic start date is 6 mos down the road. Is there a setting on the MRP type that will allow planned on demand (PD) materials to use the PDT to trigger MRP? Hopefully this explanation is clear enough.
V1 is a copy of VB in our system
Material have MRP type Z1 (ROP upto Max stock) and Lot size ZB (replenish to Max Stock + requirements). Material reorder point is 2 and Max stock 4, we have 3 on order. Why is no additional PR generated to replenish up to Max stock level?
MINI MRP means running MRP for one or particular item/items only
hi guys,
how can I be trained o become a SAP ANALIST?