Welcome to the tutorial on SAP preventative maintenance. We will explain the steps of the preventative maintenance process and show you how to execute them in the system. This tutorial is part of our free SAP PM training.
SAP preventative maintenance facilitates the process of sustaining production equipment, or technical objects, on an ongoing basis. By employing preventative maintenance, an organization can ensure high availability of production equipment for the long term. The process reduces equipment breakdowns, thus helps accomplish the following objectives:
- Reduce operating expenses
- Increase productivity
- Defer asset expenditures
SAP preventative maintenance work can be planned with respect to scope of work and scheduling can be done accordingly. The activities are stored in the form of a task list, so that they can be repeated frequently. A maintenance plan is created to define date for inspection, preventive maintenance task and repairs in advance.
The following external factors should be considered for planning preventative maintenance:
- Manufacture Company Recommendations: To follow suggested instructions and timelines
- Legal Requirements: To comply with government imposed policies
- Environmental Requirements: To avoid environmental hazards
SAP Preventative Maintenance Types
There are three types of SAP preventative maintenance as illustrated below:

- Time Based: Tasks are triggered at a specific frequency; For example, every three months or every six months
- Performance Based: Task are triggered when the specific performance level of the object is reached; For example, electric meter reading every 1500 units
- Condition Based: Task are triggered when external conditions fall within a specific range; For example, temperature outside higher than 85° C
SAP Preventative Maintenance Process
The process flow for SAP preventative maintenance is shown below and explained in the following sections:

As a preface, the components of the SAP preventative maintenance process fit together as illustrated in the following image:

Maintenance Strategy
First, a maintenance strategy is created for a piece of equipment. In this step, the sequence of planned tasks is defined. The maintenance strategy will later be assigned to a task list and maintenance plan. The strategy does not contain any date or details about the activity and technical object, and therefore can be used in various maintenance task lists and maintenance plans.
The maintenance strategy is used in both time based and performance based maintenance, since either time duration or performance level can be used as performance indicators. A common unit of measure must be identified.
Menu path | Logistics> Plant Maintenance >Preventive Maintenance > Maintenance Planning > Maintenance strategy > Change |
Transaction code | IP11 – Change |
On the details screen of transaction code IP11, enter the following details:
- Name
- Description
- Select scheduling indicator to define the type of scheduling from the following options: Time (Example: Every 2 months, not considering factory calendar); Time – key date (Example: Every 30 days on the 5th of each month); Time – factory calendar (Example: Every 60 working days per factory calendar); Performance based (Example: Every 1000 kilometers)
- Strategy unit as the unit of measure on which the scheduling calculations are done (this cannot be changed)
- Call horizon percentage to calculate the time for creating the next maintenance order or notification after the start or completion of maintenance plan (Example: If the duration of cycle is 100 days and the call horizon is 0%, the system creates an order immediately; 90% , the system creates the call after 90 days and so on)
- Shift factor to indicate by what value the tolerance period will be impacted for late or early completion of maintenance
- Tolerance for early completion to indicate by what percentage of the cycle length the completion of maintenance may be considered late or early
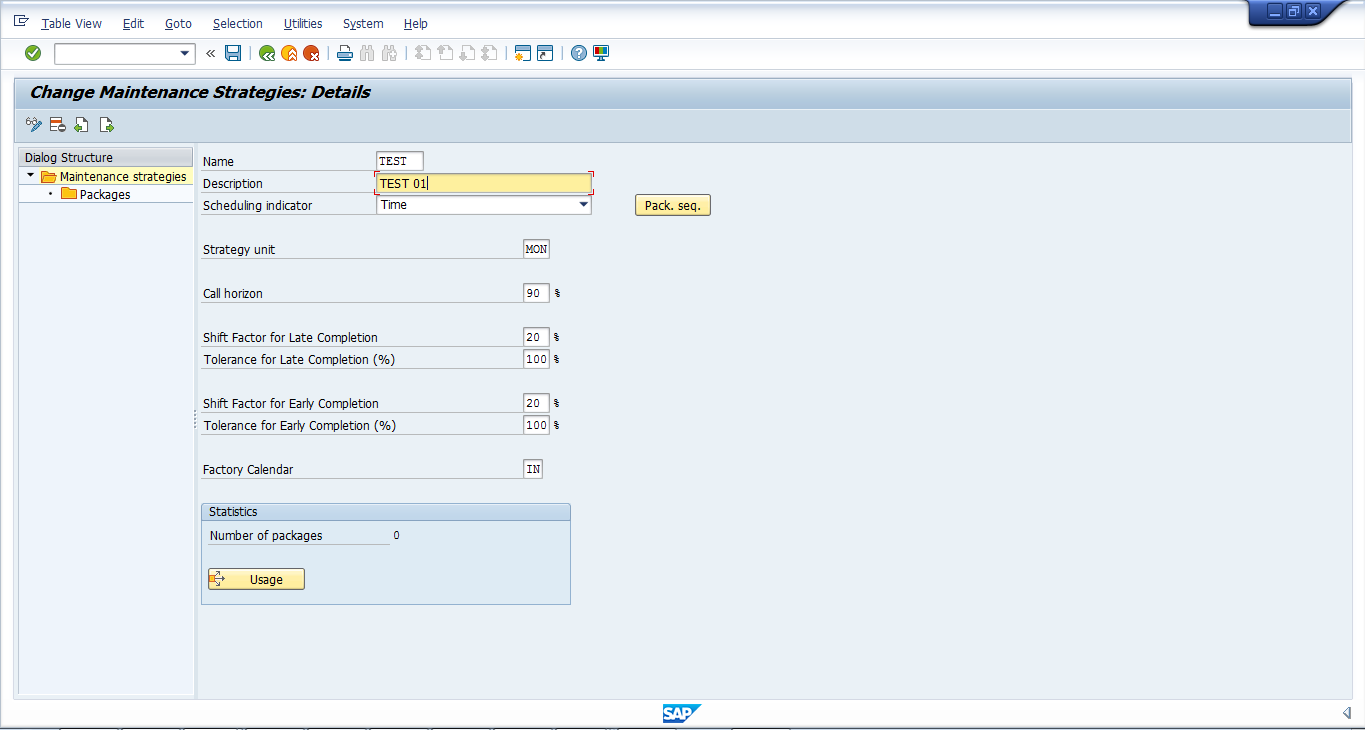
After entering all the required data, double click on packages folder. Enter the following details in the row for each package you want to create:
- Cycle length
- Unit of measure as defaulted from strategy unit
- Cycle abbreviation
- Initial lead float as the number of days which adjust the basic start date of the order
- Subsequent follow up as the number of days which adjust the basic end date of the order
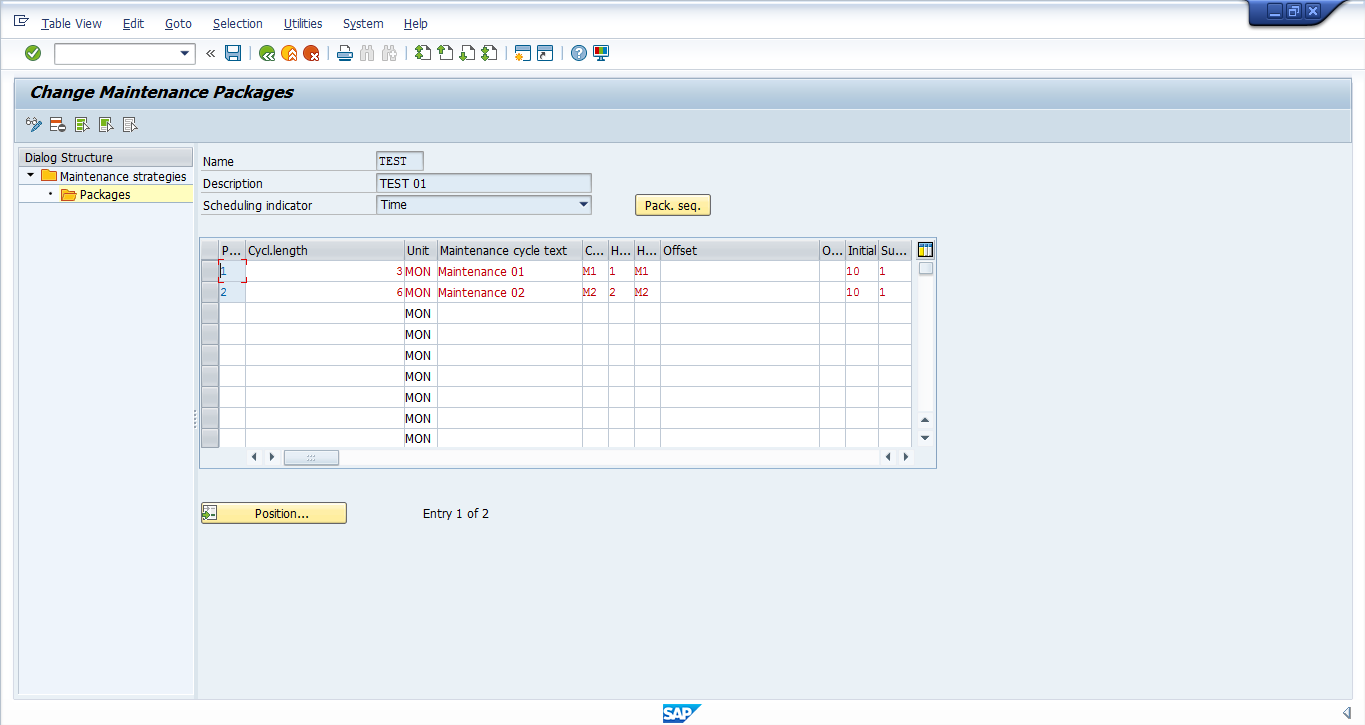
Click on the save icon to save the maintenance strategy.
Now click on package sequence button to view the package sequence scheduling, as shown below:
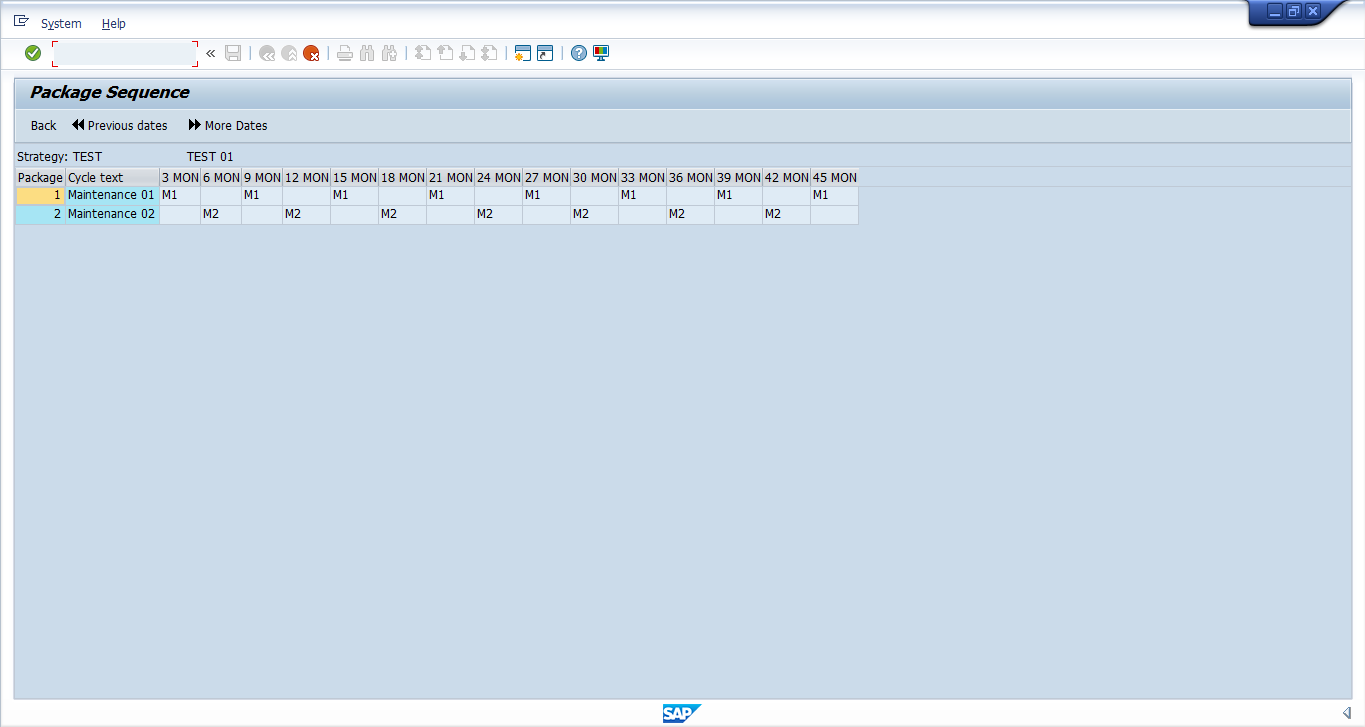
Your maintenance strategy is complete.
Task List
Now, you must create a maintenance task list and assign the maintenance strategy to it. A task list is a sequence of maintenance activities which are performed in a plant repeatedly. It is divided into three parts:
- Equipment task list
- Functional task list
- General maintenance task list
Menu path | Logistics > Plant Maintenance > Preventive maintenance > Work scheduling > Task list > for equipment > Create |
Transaction code | IA01 – Create |
On the initial screen of transaction code IA01, enter the equipment ID and press Enter to create a task list:
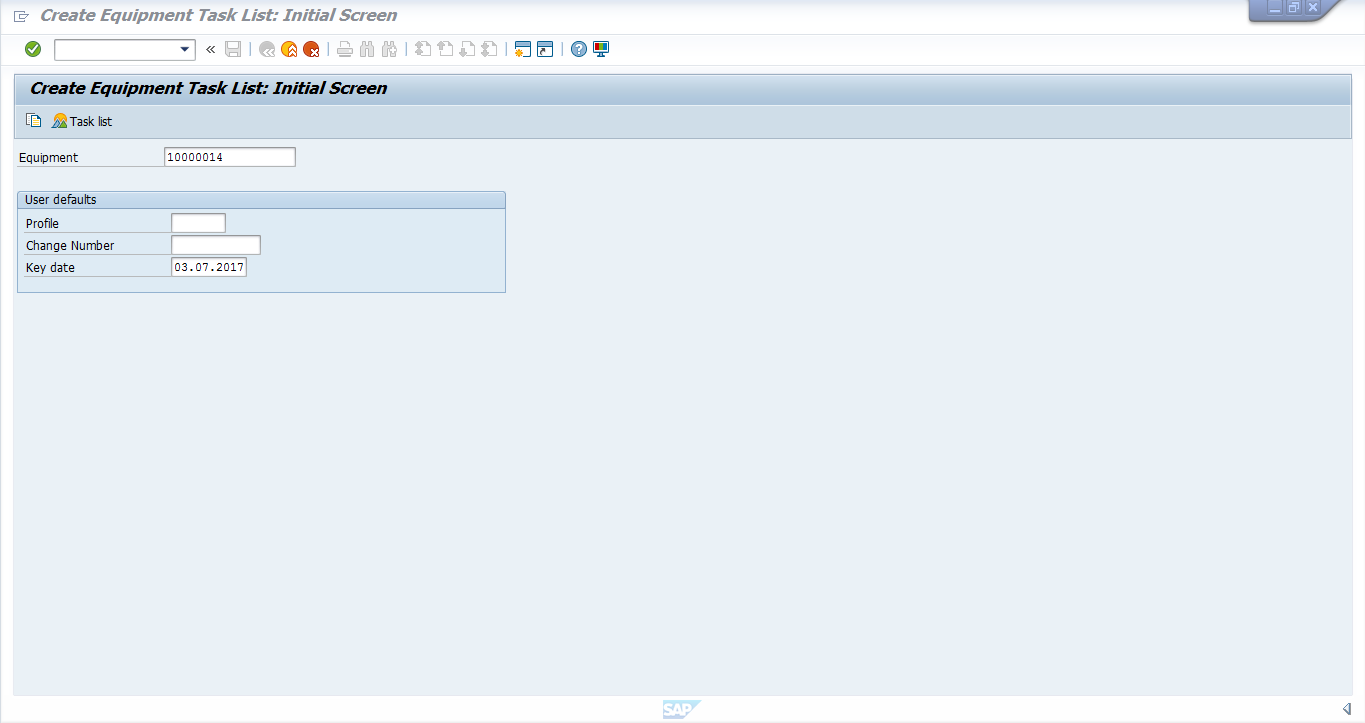
In the task list entry screen, enter the following details as a separate row for each activity in the task list:
- Work center
- Planning plant
- Control key as PM01, or you can map external service details for the operation with control key PM03
- Operation description
- Work required for task and units
- Planner group number
- Duration of task and units
- System condition
- Status of operation
- Assign maintenance strategy
Click on the save icon to save the task list.
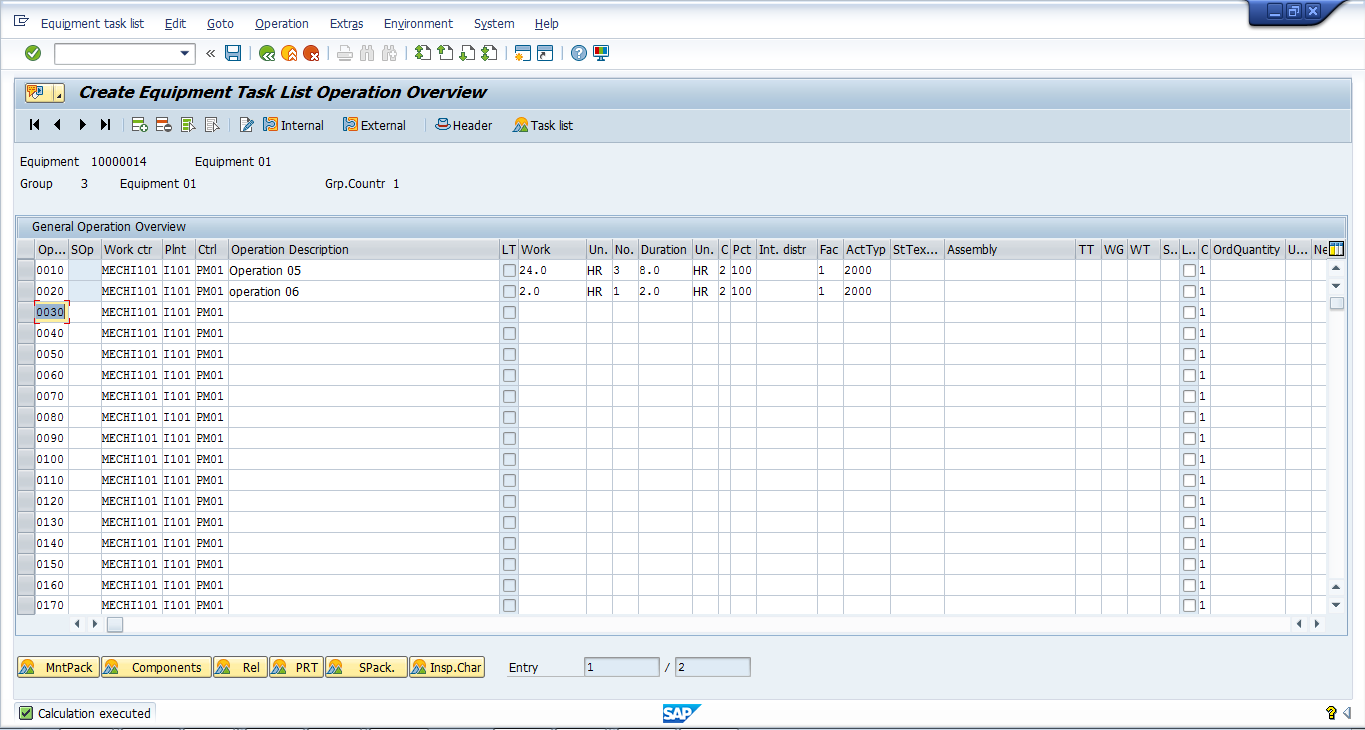
Your task list is now created.
Create Maintenance Plan
A maintenance plan is created for all equipment. It contains the scheduling information created for the maintenance of the equipment.
Menu path | Logistics > Plant Maintenance > Preventive Maintenance > Maintenance Planning > Maintenance Plans > Create > Single Cycle Plan |
Transaction code | IP41 – Single Cycle Plan |
On the initial screen of transaction code IP41, leave Maintenance plan field blank to allow the system to automatically assign a number. Specify Maintenance Order as maintenance plan category.
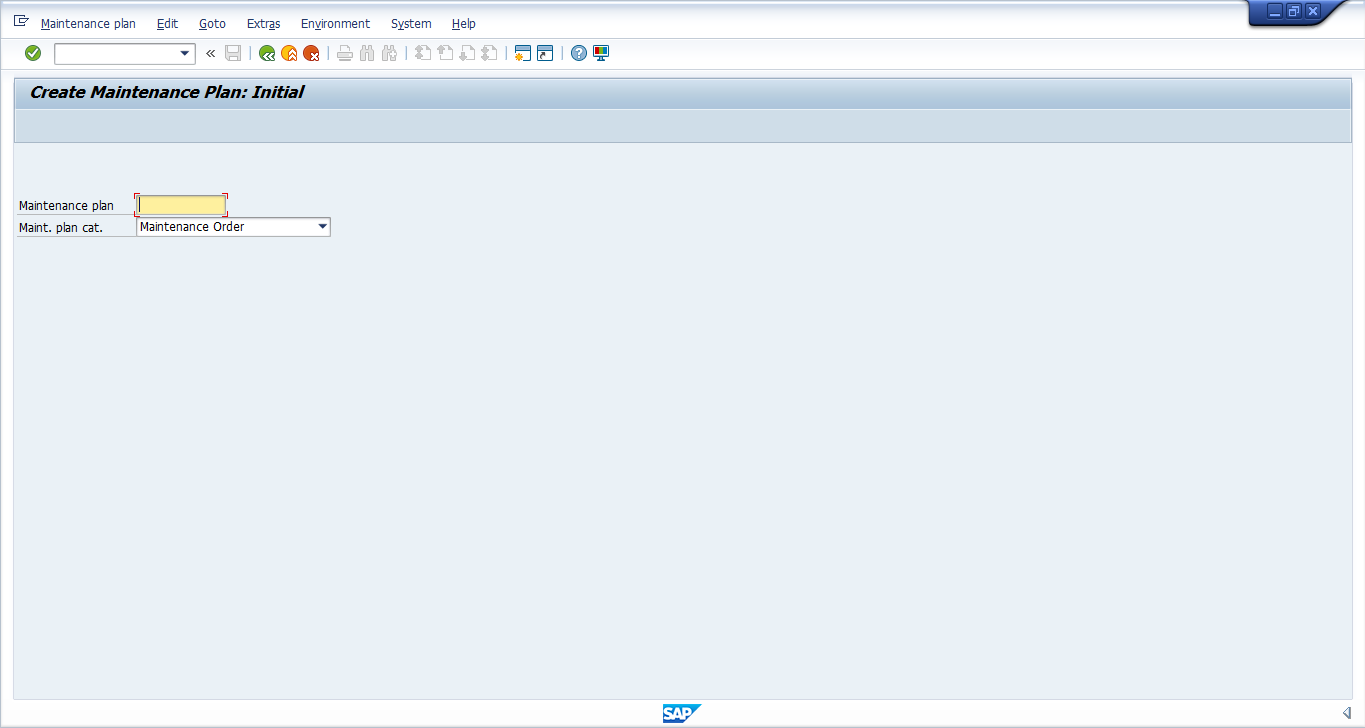
Press Enter to enter the plan details. Enter a description for the plan, and cycle text in the Maintenance plan cycle tab in the top pane, as below:
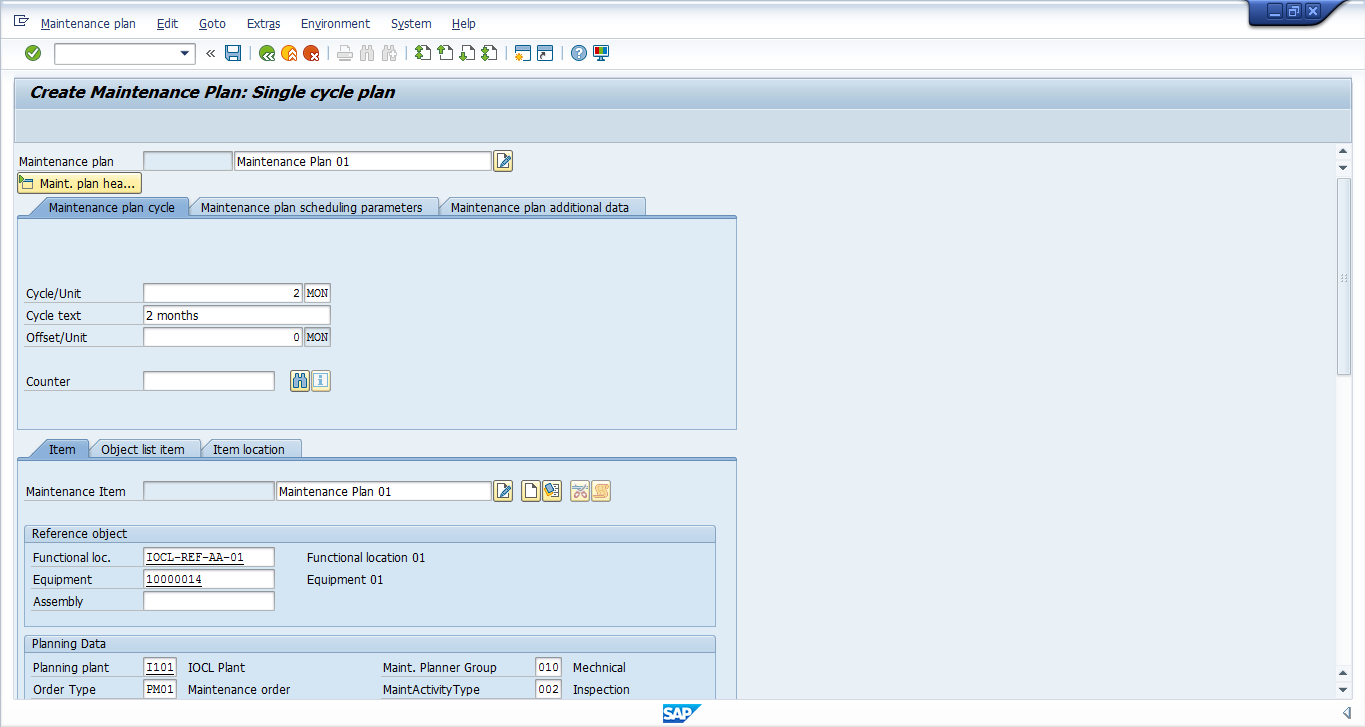
Scroll down to the Item tab of the bottom pane and enter the following details:
- Functional location
- Equipment number
- Planning plant
- Maintenance planner group
- Order type
- Work center
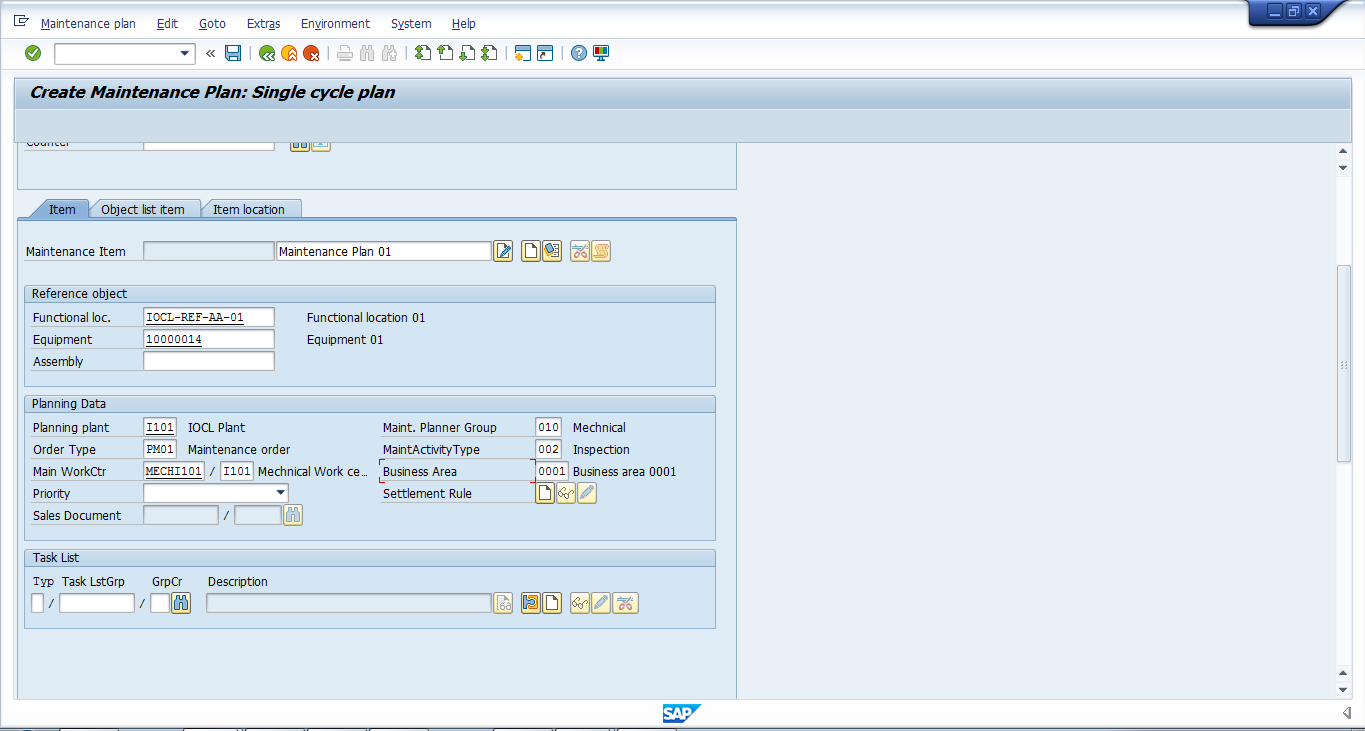
Next, assign the task list by clicking the task search button in the Task List section. In the resulting screen, search relevant task lists by entering the equipment/functional location combination. Select the tasks you want to include in the maintenance plan and execute.
Click on Maintenance plan scheduling parameters tab in the top pane and enter the following information:
- Cycle modification factor
- Call horizon percentage to calculate the time for creating the next maintenance order or notification after the start or completion of maintenance plan
- Scheduling period and units
- Date of start of cycle
Click on the save icon to save the maintenance plan.
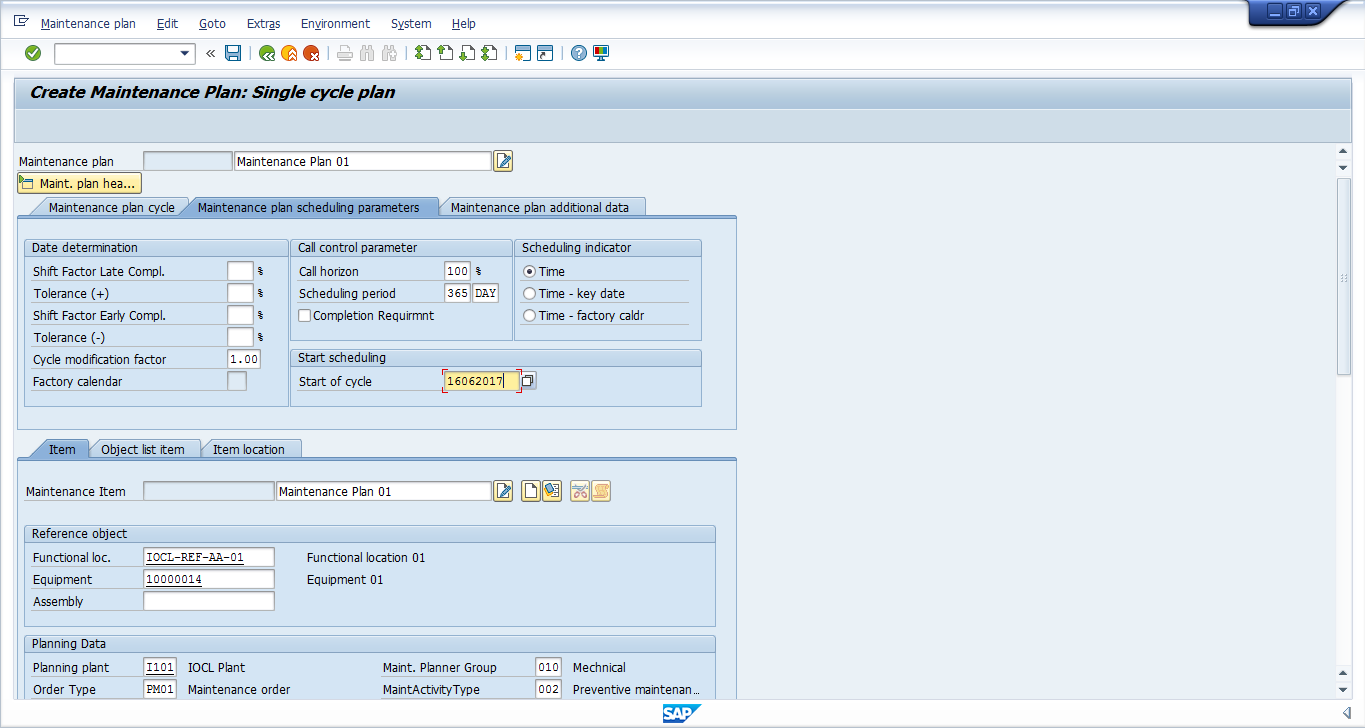
You will be provided with a maintenance plan number. Take note of this number for scheduling. The maintenance plan is now created with the task list assigned.
Schedule Maintenance Plan
Menu path | Logistics > Plant Maintenance > Maintenance Planning > Scheduling for Maintenance Plans > Schedule |
Transaction code | IP10 – Schedule |
Specify the maintenance plan created in the last step. Click the Start button in the menu bar to pull up the schedule.

Now, select the first row from the scheduling list and release it by clicking on the release call icon .
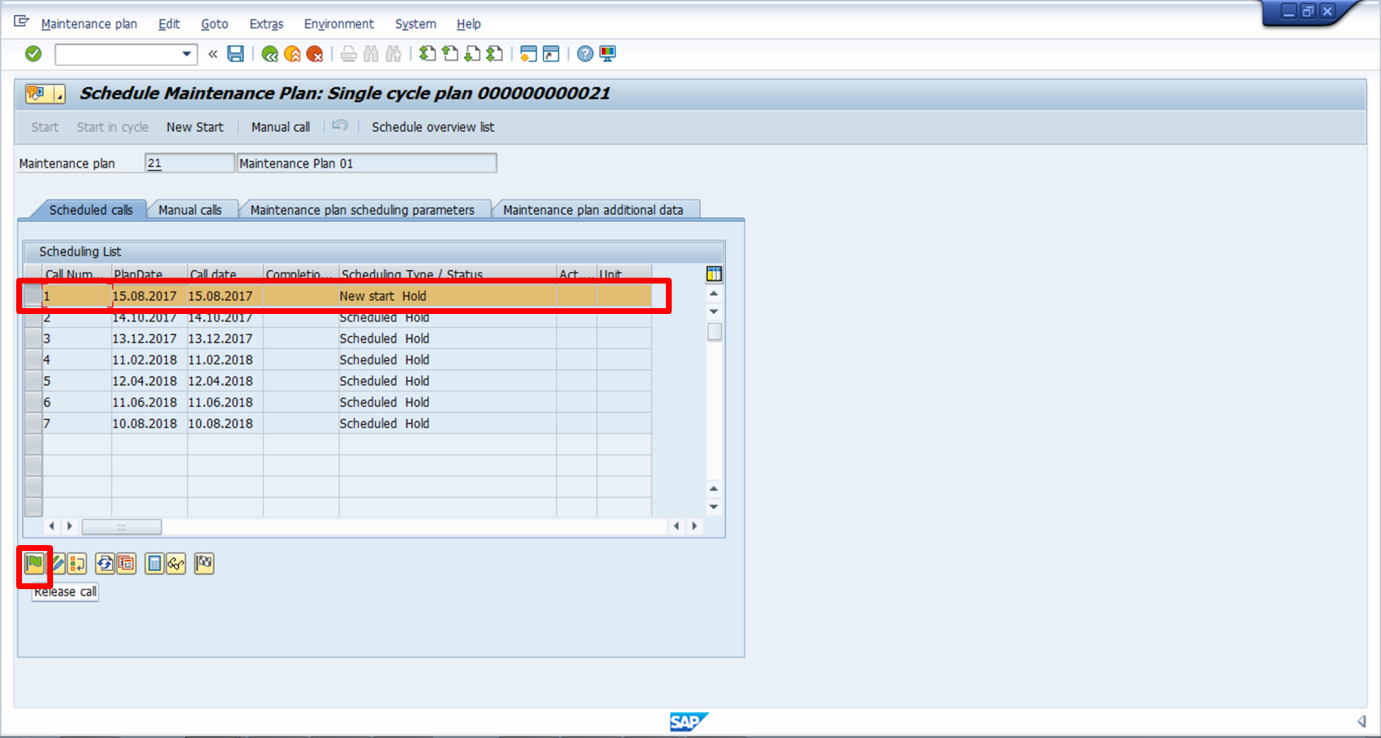
Click on the save icon to save the schedule maintenance plan.
Maintenance Order
The maintenance order is automatically created through maintenance plan scheduling. We will first identify the order number by running a report of all maintenance plan schedule items. Then we will release the order to indicate that the maintenance activity is actually being performed.
Identify the created order number in transaction code IP24.
In the initial screen, enter known selection criteria, such as period or maintenance plan number.

Click execute to view the report.
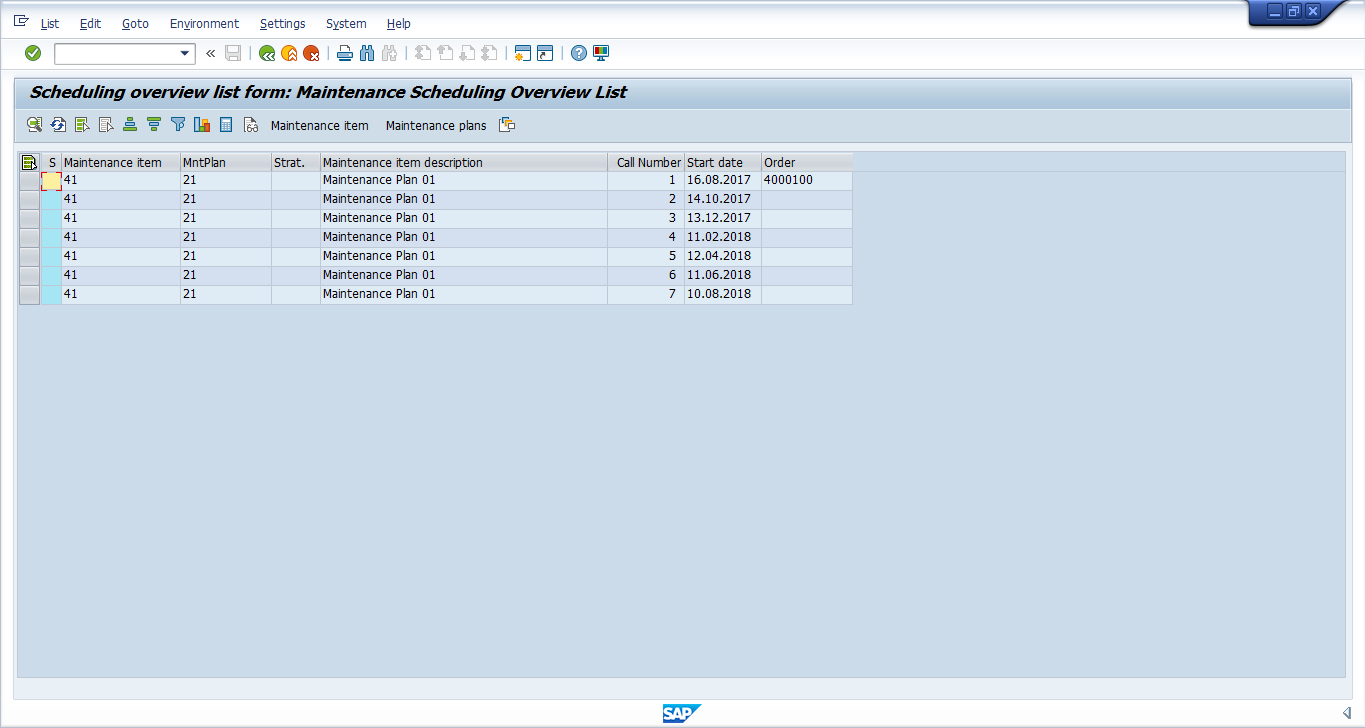
Take note of the order number for your maintenance schedule item.
Now as the maintenance task is being performed, you must release the maintenance order. Open the order through transaction code IW32.
Specify the order number to pull up the order in change mode. Click the release icon .
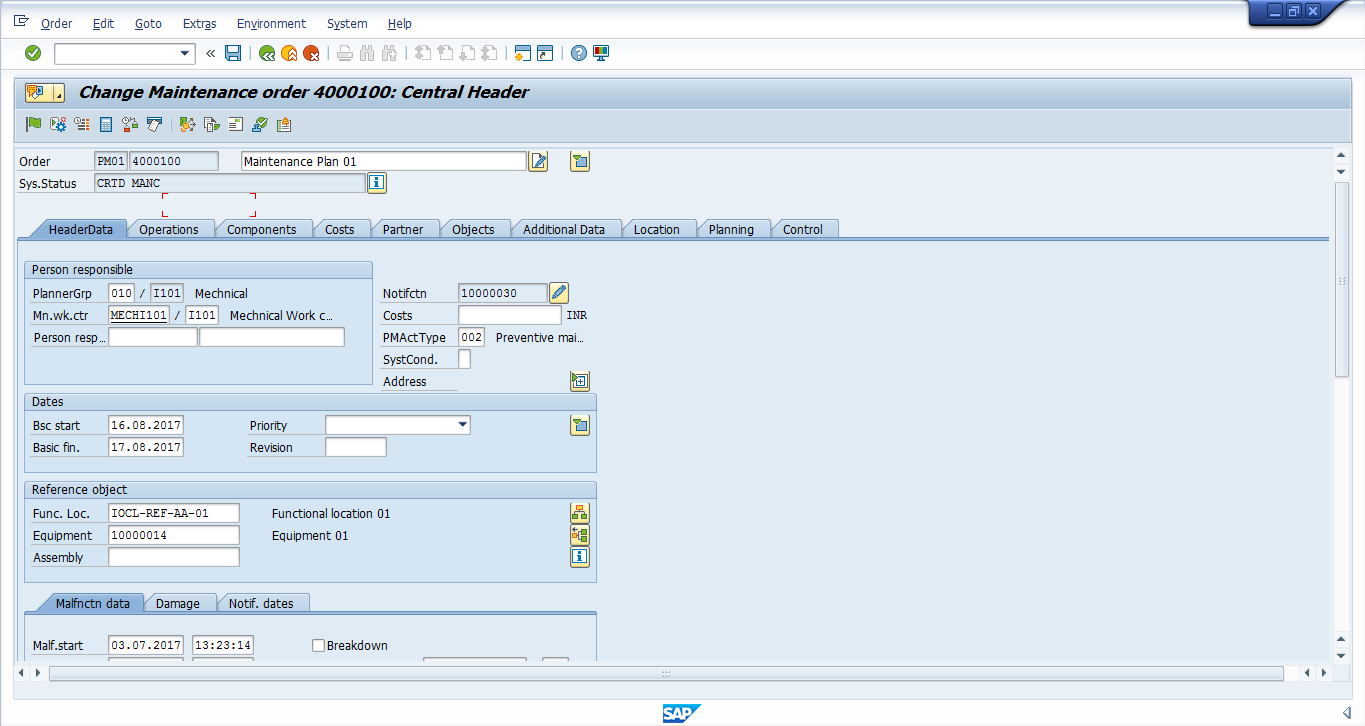
The maintenance order is released and system status is changed to REL.
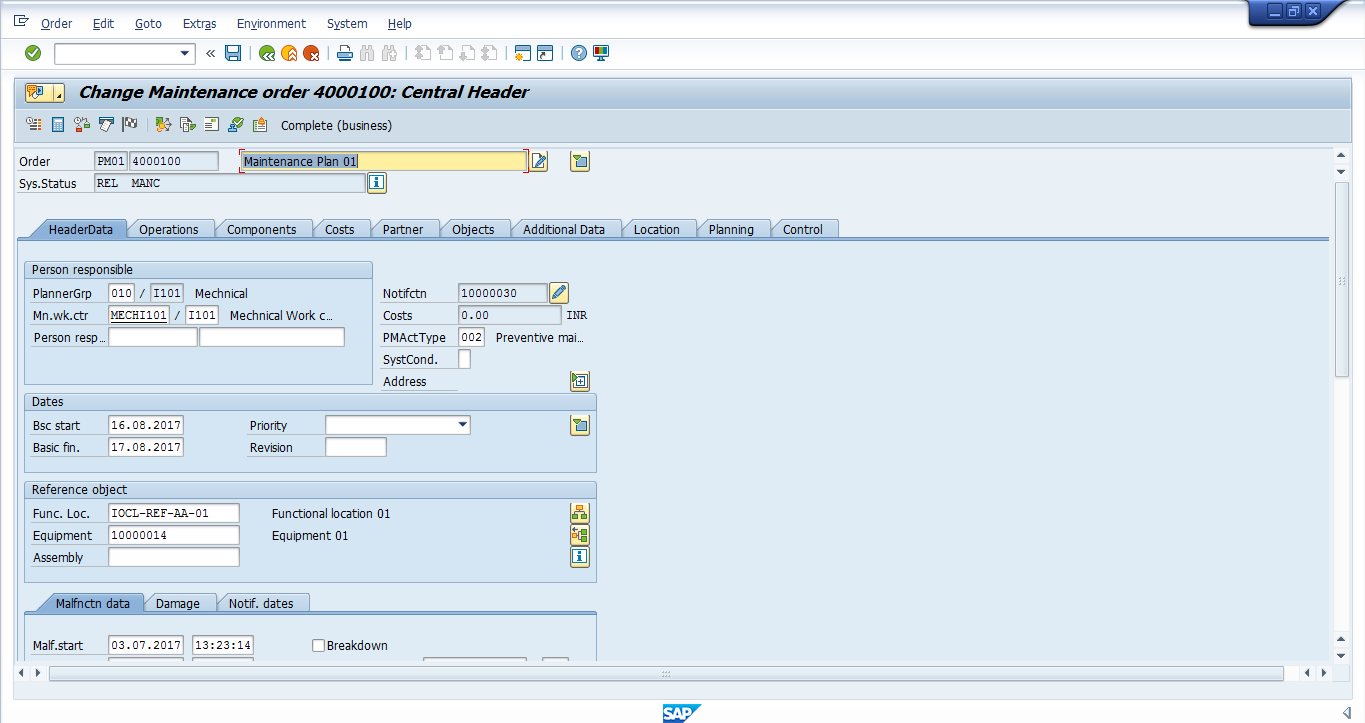
Technical Completion and Settlement
Now, we have to enter actual work performed on the maintenance activity/task by creating a confirmation. After entering a confirmation, the operation will get confirmed or partially confirmed. Enter work via transaction code IW41.
On the initial screen, specify the order number and press Enter to continue:
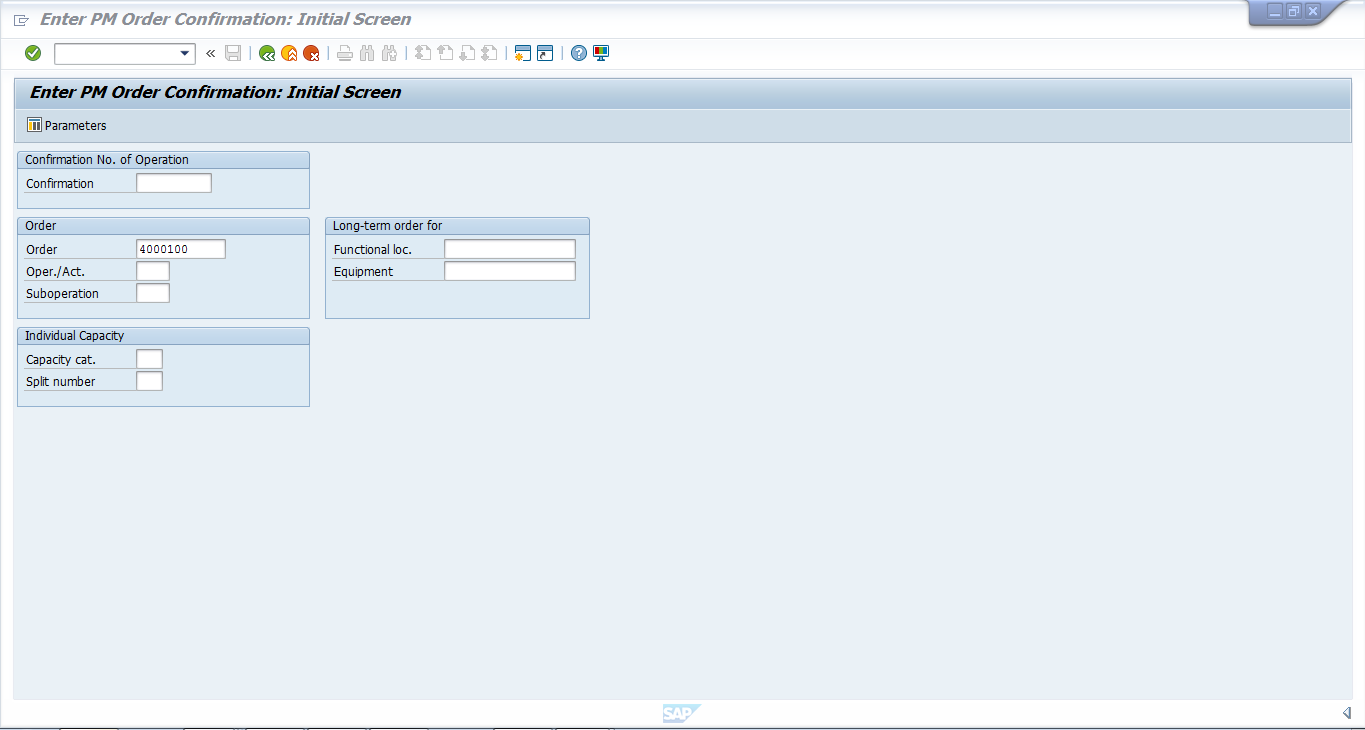
Enter the following actual data:
- Work center (this is defaulted from maintenance plan)
- Actual work and units
- Work start and finish dates/times (optionally update; work finish is defaulted with system date/time)
Click on the save icon to save the confirmation.

Technical Completion
Once all work has been confirmed on the order, change the status to technically complete. Open it in change mode through transaction code IW32.
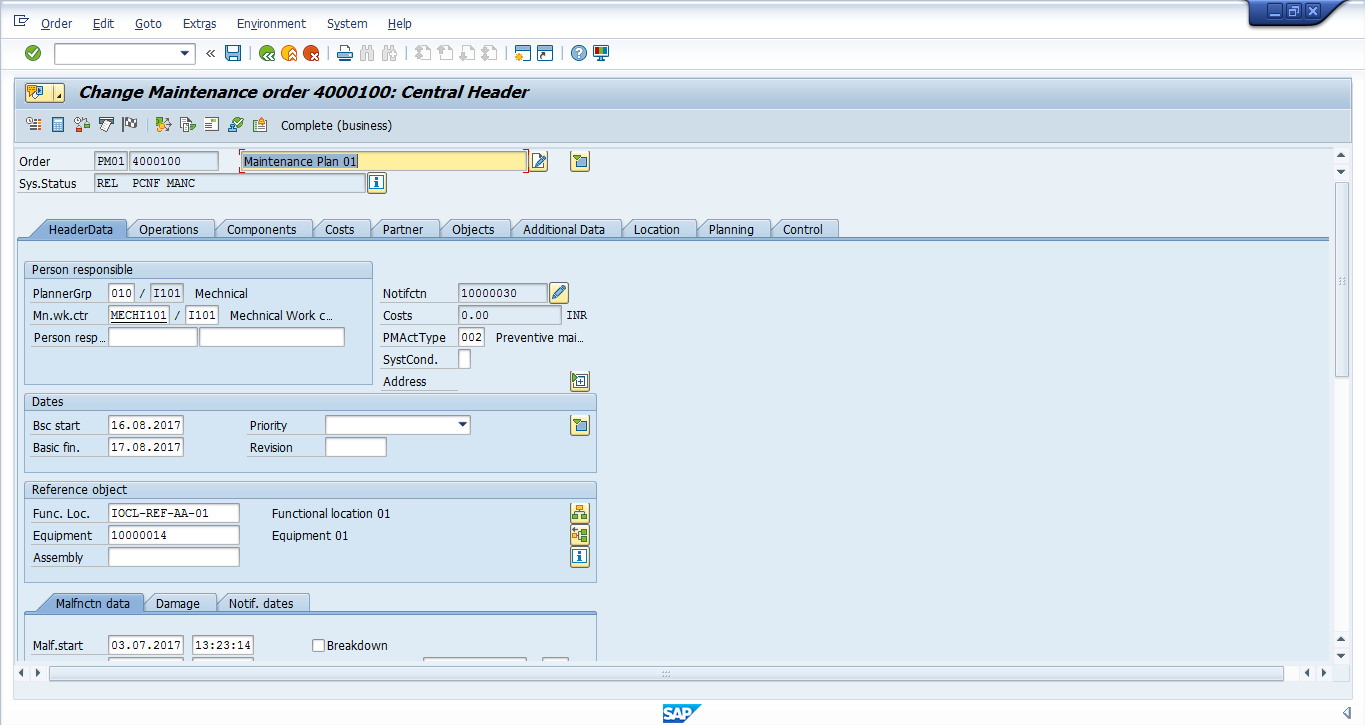
Click on the technically completed flag in the menu bar. The maintenance order system status will be updated to TECO as shown below:
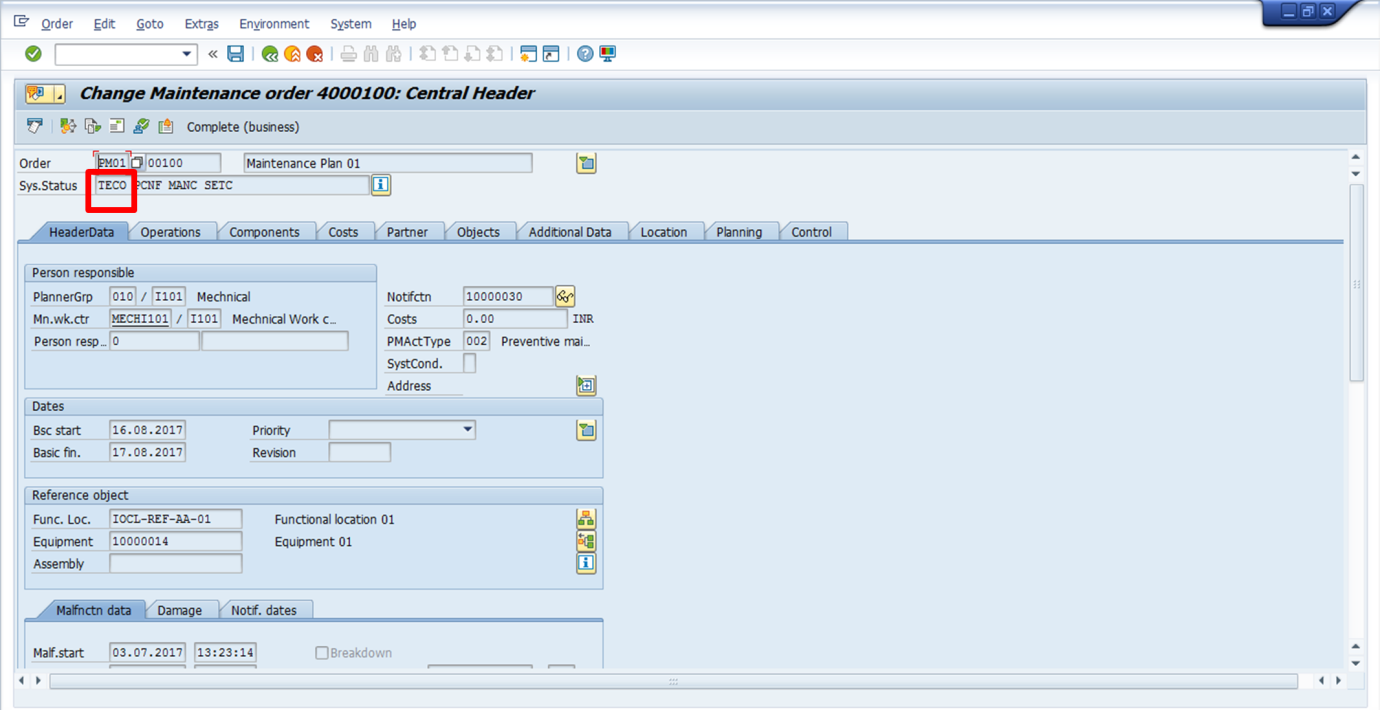
Settlement
Menu path | Plant Maintenance > Maintenance Processing > Completion > Individual Processing > Settle |
Transaction code | KO88 – Settle |
On the initial screen of transaction code KO88, enter the following:
- Maintenance order number
- Settlement period
- Fiscal year
- Select Test Run tickbox
Click execute to run in test mode and check your entries.

Check the settlement for errors. If everything is correct, go back and remove the Test Run tickbox and re-execute:
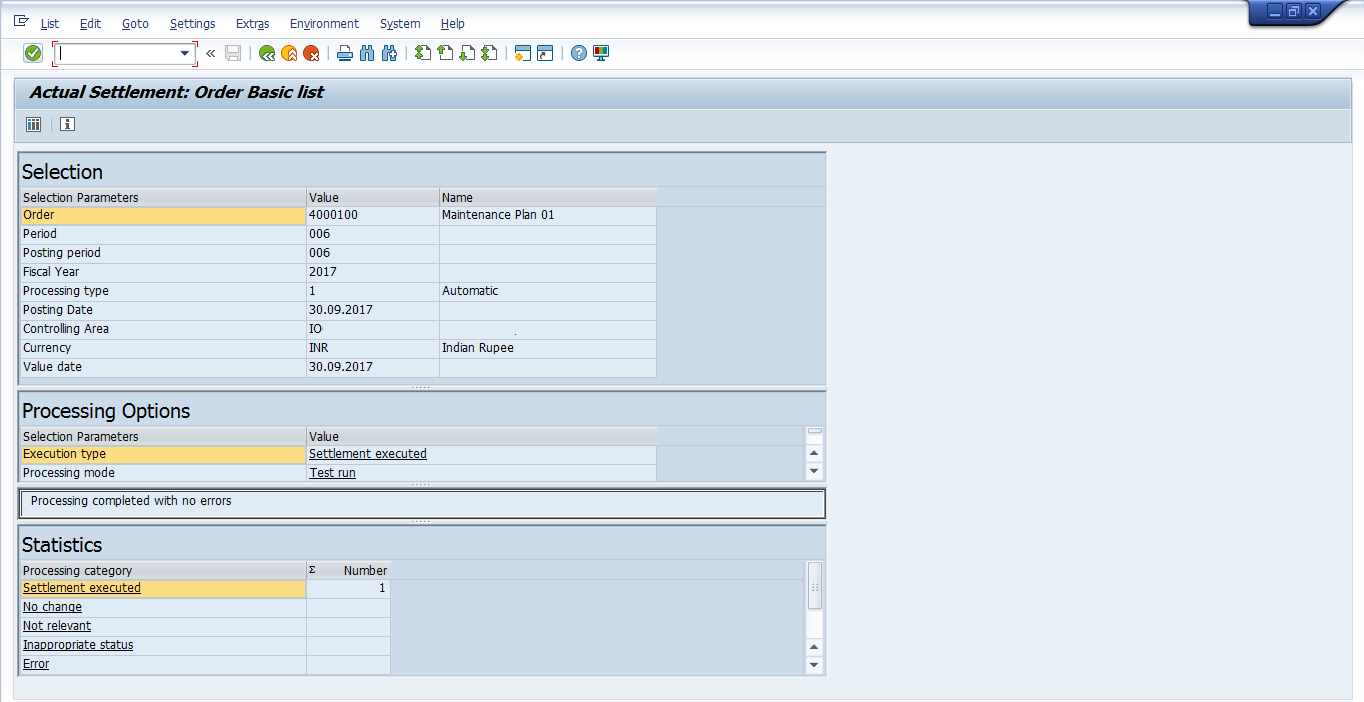
The actual cost incurred to complete the maintenance tasks will be settled to the respective cost centers.
—
Did you like this tutorial? Have any questions or comments? We would love to hear your feedback in the comments section below. It’d be a big help for us, and hopefully it’s something we can address for you in improvement of our free SAP PM tutorials.
Navigation Links
Go to next lesson: SAP PM Task List
Go to previous lesson: SAP Refurbishment Order
Go to overview of the course: SAP PM Training
I have a key date suppression maintenance plan with different maintenance item packages. The jobs must be done in a 2 week period, so the maintenance items must be split in 2 week period. How can I get this done?
Nice and easy to follow. Thank you.
Hi Team,
I love all the modules that are explained on this website and it has become my go-to website whenever I start a new module. But I think, in the preventive maintenance strategy, the definition of shift factor and tolerance got exchanged with each other. I think shift factor should be 100% and tolerance should be 20%. Do let me know in case of any concerns.
Nice explanation and easy to understand.
I am trying to make a 12 week suppressed PM into a 24 week suppressed PM. Any help is appreciated.
Team
I have 20 number of maintenance plans which can genereate every month, i have done techo 16 work orders
So remaining 4 is pening
Any T-Code is availble to check the Actual work orders genreate Vs Techo orders ?
Can we show compliance through SAP system itself ?